joe_merchant
Regular Contributor
I have the AQ280 out drive. Over time, it started sporadically not working, i.e., sometimes it worked, and other times it didn't. Finally quit working, although both relays did click at that time. Pulled the mechanism, cleaned everything up, changed the bearings, and tested it again. On the bench, the motor works fine in both directions by jumping the leads with a battery. Bench tested both relays, and they tested good. Put it back in the boat, and it only clicks in the up direction. Just to be sure, bought new relays, installed them, and now nothing. That is with the black box removed from the lift mechanism so being on too tight wouldn't be an issue.
Am assuming that I need to start with power from the helm, and see what is getting back to the wiring harness. I have the below wiring diagram. It gives me the basics so that I can get started, but mine is the two wire, not the four wire shown.
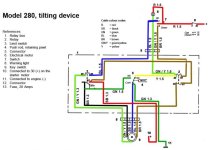
I can get back to the connector, but want to test further. Anyone have a wiring diagram for the 2 wire system? Am assuming that I need to check the limit switch. It clicks and moves freely, just haven't tested it electrically yet. Also noticed that it lists item #13 as a fuse but I don't physically see it in my arrangement. Anyone know where I should be looking for this, and if most actually have a fuse?
And, of course, the new relays are too tall to allow the cover to go on, but I'll deal with that later.
Thanks in advance for the help.
Am assuming that I need to start with power from the helm, and see what is getting back to the wiring harness. I have the below wiring diagram. It gives me the basics so that I can get started, but mine is the two wire, not the four wire shown.
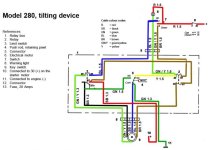
I can get back to the connector, but want to test further. Anyone have a wiring diagram for the 2 wire system? Am assuming that I need to check the limit switch. It clicks and moves freely, just haven't tested it electrically yet. Also noticed that it lists item #13 as a fuse but I don't physically see it in my arrangement. Anyone know where I should be looking for this, and if most actually have a fuse?
And, of course, the new relays are too tall to allow the cover to go on, but I'll deal with that later.
Thanks in advance for the help.
Last edited: