Akjohn
Contributing Member
Has anyone seen this fitting before? if so can you make sense of it?
This oil line came off the back of a 1977 360/250hp, the male end of the brass T screws into the main oil galley just north of the intake manifold.
All three connections on the T are 1/8" NPT, so one side to the motor, one had a plug in it and the other had the wire bound rubber hose screwed into it. The wire bound rubber hose fed the cast aluminum bracket that the two oil sensors attach to, also attached to the casting is the drain hose (which is the only usefulness that makes any sense to me).
The problem I have is where the wire bound hose attaches to the brass T, the T should have a inverted flare (female) to keep it from leaking, the weird thing is I have two identical motors that I picked up second hand. (I have not run them in a boat...yet), in any case on one of the motors this line did NOT leak and the other it did.
So, this does not look right to me as you can use a flare fitting if it does not have a seat to tighten against, yet I suspect this has been this way for many moons, the fitting does appear to be 1/8" NPT and it can be tightened in the brass T, however the hose will still turn.......?
Any thoughts...........?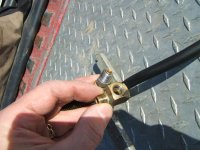
This oil line came off the back of a 1977 360/250hp, the male end of the brass T screws into the main oil galley just north of the intake manifold.
All three connections on the T are 1/8" NPT, so one side to the motor, one had a plug in it and the other had the wire bound rubber hose screwed into it. The wire bound rubber hose fed the cast aluminum bracket that the two oil sensors attach to, also attached to the casting is the drain hose (which is the only usefulness that makes any sense to me).
The problem I have is where the wire bound hose attaches to the brass T, the T should have a inverted flare (female) to keep it from leaking, the weird thing is I have two identical motors that I picked up second hand. (I have not run them in a boat...yet), in any case on one of the motors this line did NOT leak and the other it did.
So, this does not look right to me as you can use a flare fitting if it does not have a seat to tighten against, yet I suspect this has been this way for many moons, the fitting does appear to be 1/8" NPT and it can be tightened in the brass T, however the hose will still turn.......?
Any thoughts...........?
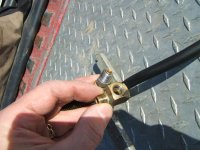
Attachments
Last edited: